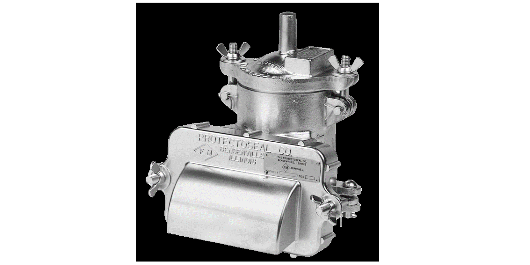
Induchem Group are an authorized supplier of Protectoseal in Ireland. We supply a wide range of tank protection equipment. The case study below will explain how Protectoseal’s products can be used in the safe production of alcoholic beverages.
Production of Alcoholic beverages can be classified into two major categories based on their mode of preparation; fermented beverages (e.g. wine and beer) and distilled spirits (e.g. whiskey and brandy). In both cases, sugar from the raw material (e.g. grains, fruits, sugar can juice, etc) is extracted and converted to alcohol and carbon dioxide through the fermentation process.
Distilled spirits undergo additional processing – specifically passing through the “still” where alcohol concentrations can be above 90% by volume (ABV). Vapors and gases released throughout the distillation and alcohol production processes may present toxic and explosive risks if not managed properly. Section 3-4.10.2 of the Recommended Fire Protection Practices for Distilled Spirits Beverage Facilities (published by The Distilled Spirits Council of the United States, Inc.) states that “each still should be protected for excess pressure and vacuum. It is recommended that all vents to the outside, and especially vents from vent condensers be equipped with flame arresters.”
Pure ethanol, the alcohol that is present in distilled spirits has a flashpoint (temperature at which liquids give off enough vapor to ignite in air) of 55 degrees F; an 80-proof distilled spirit contains 40% ABV and has a flashpoint of 79 degrees F – just above room temperature. With the distillation process itself requiring heat and taking into consideration other unintended ignition sources (e.g. mechanical / electrical generated sparks, static electricity, lightning, etc.) a potentially hazardous, flammable environment may be present.
The breadth of regulations associated with the construction and operation of distilleries are often complicated and not particularly specific to the industry. Of the relevant codes and standards, compliance to the National Fire Protection Agency’s Flammable and Combustible Liquids Codes (NFPA 30) and / or ATEX 1999/92/ EC Directive is very important to ensure that the workplace is safe from fire and explosive risks. The Protectoseal Company has a long and established history partnering with the Wine and Spirits Industry to enhance operational safety and efficiency through product innovation and the promotion of industry best practices. Our work with the various international standardization bodies and an absolute adherence to ISO 28300 and API 2000 – Standards for venting atmospheric and low-pressure storage tanks as well as ISO 16852 – International standard for flame arresters, forms the cornerstone of our “Safety without Compromise” modus operandi.
Our pressure and vacuum relief vents, emergency vents and flame arrester product lines are integrated into distilleries worldwide to help safeguard against the hazards associated with the handling and storage of their flammable liquids. Protectoseal’s Series 830 Combination Pressure Vacuum Relief Vent and Flame Arrester offers a unique dual function design in an integrated, single body housing.
This innovative design delivers exceptional performance at a fraction of the footprint associated with traditional installations. Other notable features include certified low leakage pallet design, easy inspection and maintenance “swing bolt” access and a precise yet robust parallel plate arrester element design. For higher volume producers where the vapor is captured through a manifolded piping system, Protectoseal offers a series of In-Line Detonation Arresters designed to handle the more severe flame fronts which may result from those installations.
The Series 7800 Emergency Vent has exceptional flow performance, required to provide emergency relief capacity beyond that furnished by the pressure relief vent operating
under normal conditions. Low leakage is achieved through the Air-Cushion Seat design – tested, certified with a test report accompanying each unit shipped.
In the ideal world, fire and explosive risks in distilleries can be eliminated by the avoidance of flammable atmospheres and/or avoidance of ignition sources. In the practical sense however, neither of these factors can be completely eliminated. Where a flammable or explosive environment exists, and an ignition source cannot be completely avoided, explosion protection with explosion isolation is required. The correct selection and proper use of venting and explosion isolation devices serves to help mitigate the overall risks. With over 95 years in the Industry, we welcome the opportunity to work with clients to develop the most suitable vapor and flame control solution for their operational needs.
For more information on Protectoseal products and their uses for distilled spirits applications, please call your local Induchem Group representative at 021-4848900.